Technologie firmy ENRESS k energetickému využití vytříděných složek komunálního odpadu
Autoři:
doc. RNDr. Miloslav Bačiak Ph.D., ENRESS s.r.o Praha,
Jaroslav Pátek, ENRESS s.r.o Praha
Souhrn
Firma ENRESS s.r.o se několik let zaobírá problematikou energetického využití organických odpadů, a to v současné době hlavně vytříděného komunálního odpadu a kalů z čistíren odpadních vod. Firma má v Dubenci u Příbrami své detašované pracoviště, včetně laboratoří.
Klíčová slova:
odpad, kal, termická depolymerizace
Představení společnosti ENRESS
Společnost ENRESS s.r.o. je nováčkem v oblasti odpadového hospodářství. Její pracovníci se však v dané oblasti pohybují již řadu let. Firma ENRESS má ve svém portfoliu tři oblasti a to:
- Hnojiva a plnění nitrátové směrnice EU
- Prostředky ke zlepšení výtěžnosti bioplynu v BPS na chemické bázi
- Termické procesy (pyrolýza, depolymerizace)
Ve svých laboratořích v Dubenci u Příbrami a v Havlíčkově Brodě má k dispozici přístrojové vybavení k analýze plynných, kapalných a pevných složek z termické depolymerizace. V Dubenci u Příbrami jsou k dispozici 2 jednotky termické depolymerizace a to 5 l vsázková a poloprovozní šneková s kapacitou 50 kg/h vsázky. Na těchto zařízeních se vykonávají komerční testy různých organických odpadů (digestát z bioplynových stanic, odpad z výroby pektinu, pneumatiková drť, komunální separované odpady, kapalné odpady).
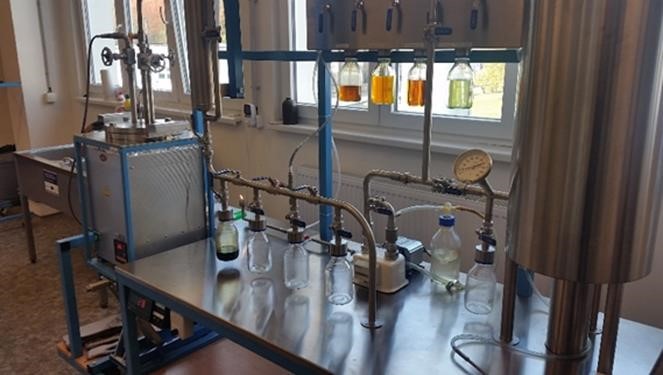
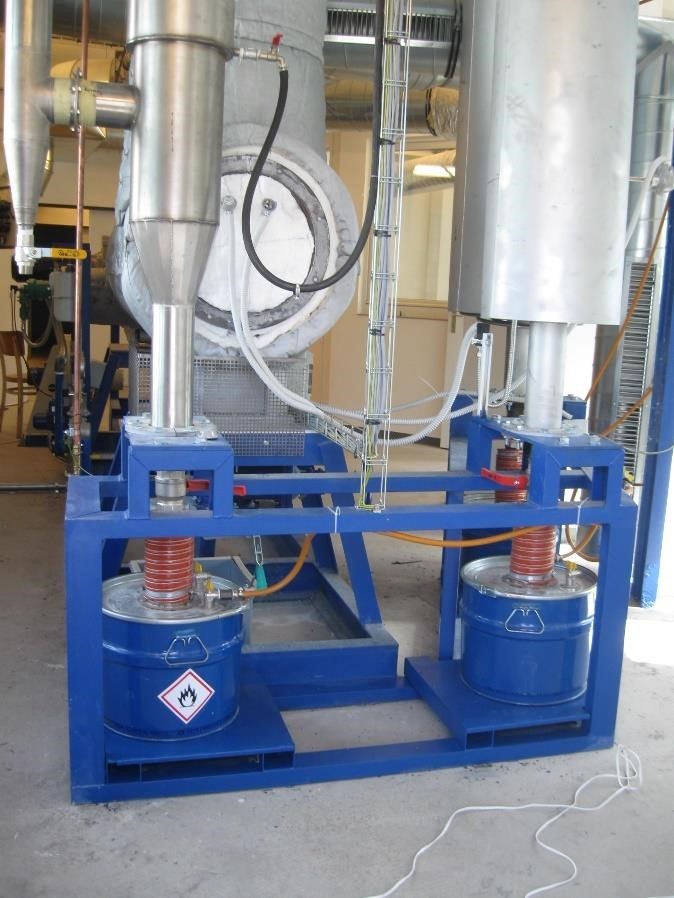
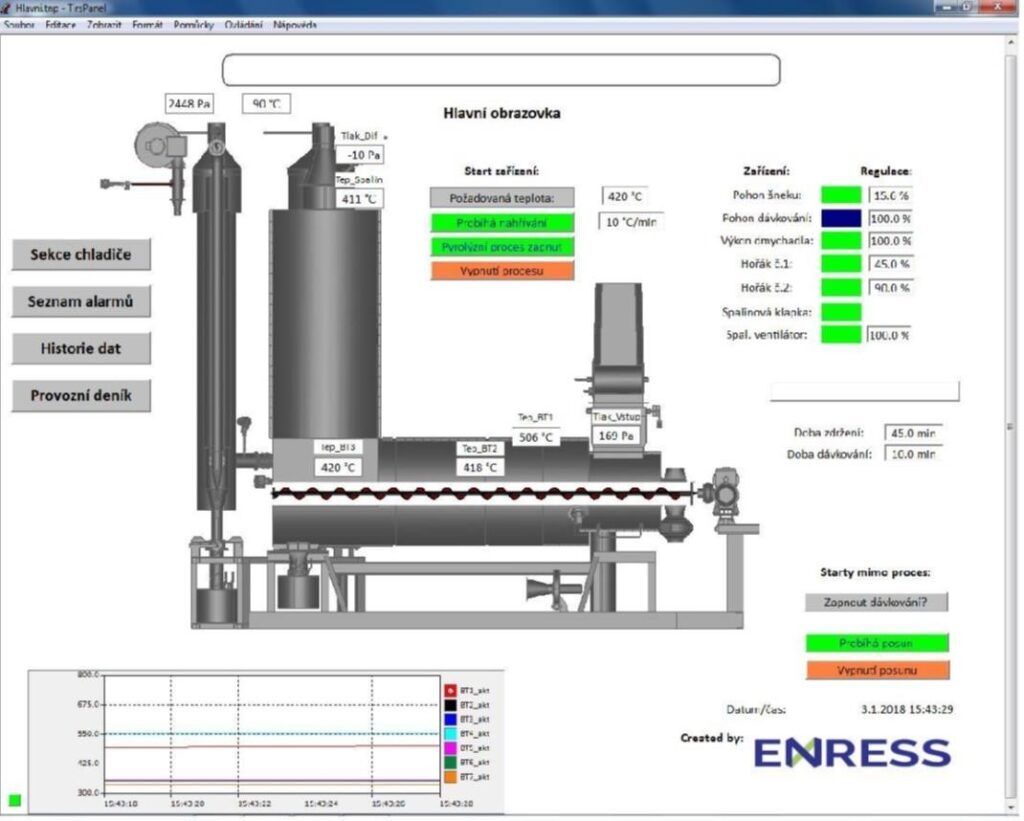
Řešení problematiky ověření možností ohřevů retorty
Experiment
V současné době řešíme ve firmě ENRESS výstavbu laboratorní šnekové retorty s dávkováním pomocí extruderu a vynášením uhlíku pomocí dalšího extruderu. V pracovní verzi jsou navrženy tři možná řešení ohřevu dané retorty, a to plynem z procesu termického rozkladu, odporovými elementy a indukcí.
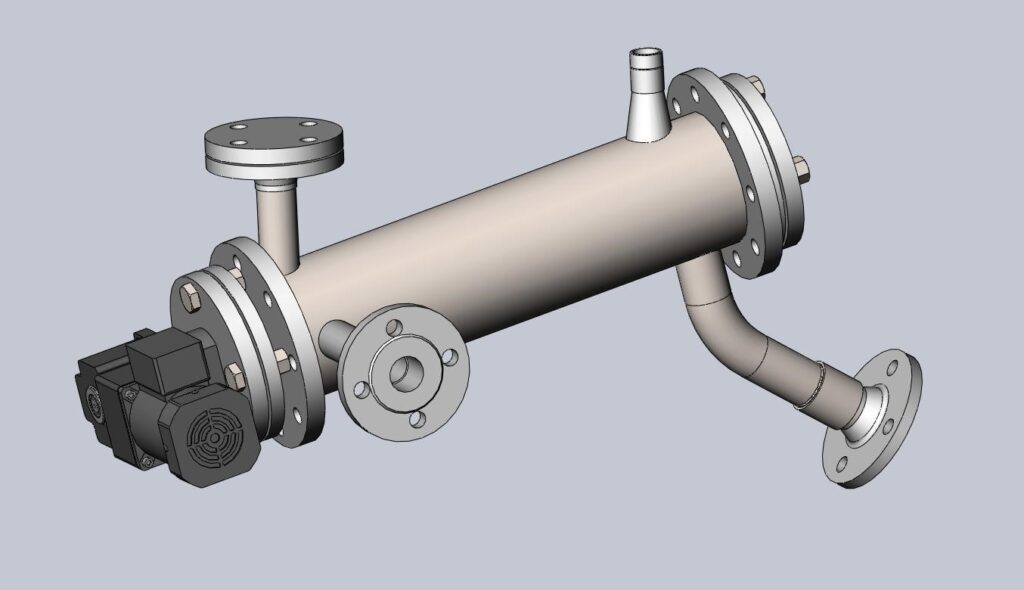
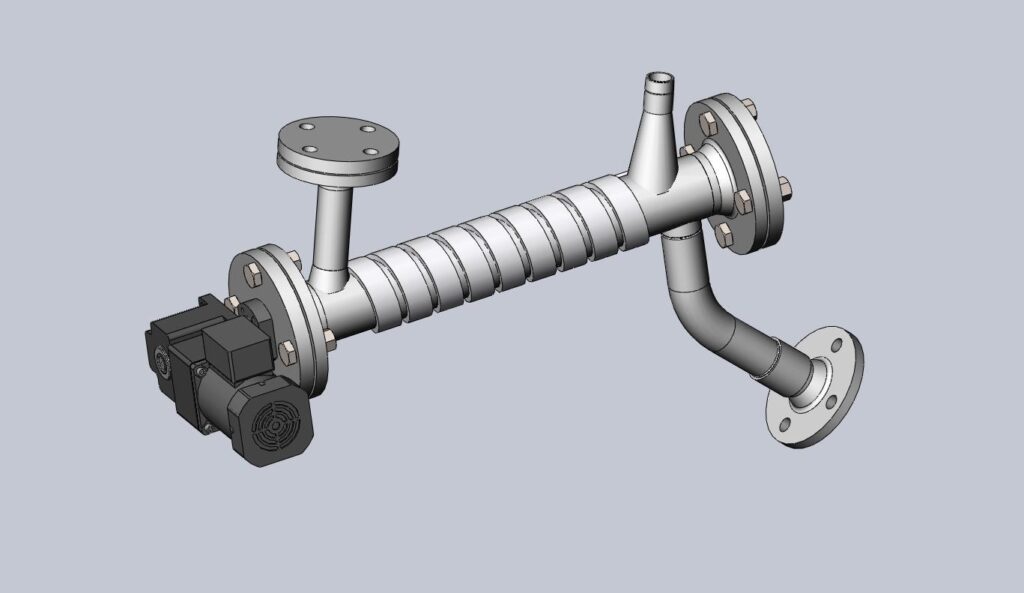
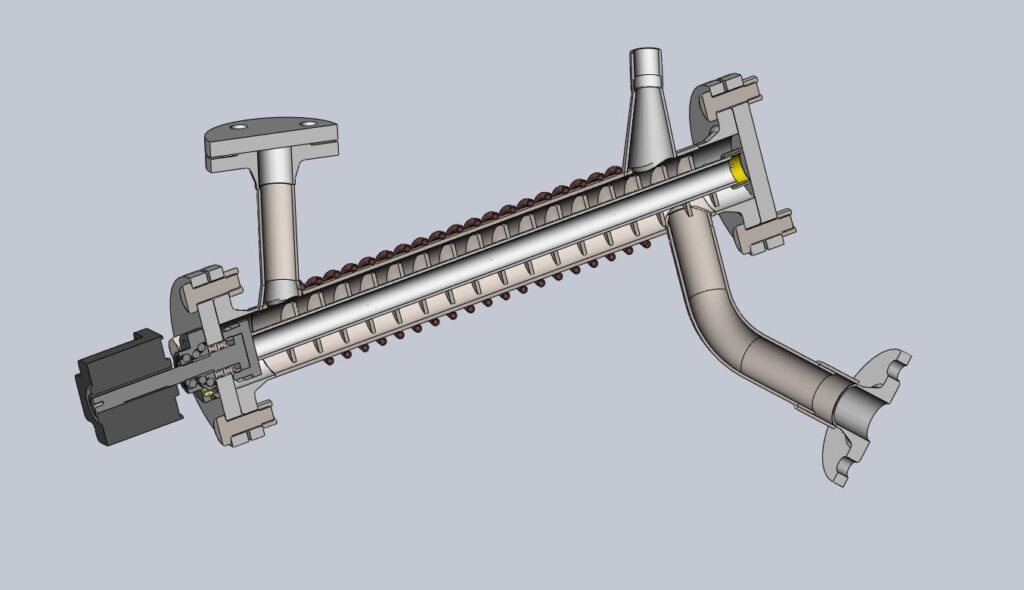
Jednotka bude do budoucna řešena s indukčním ohřevem, který se zdá být pro daný typ reaktoru nejvhodnější.
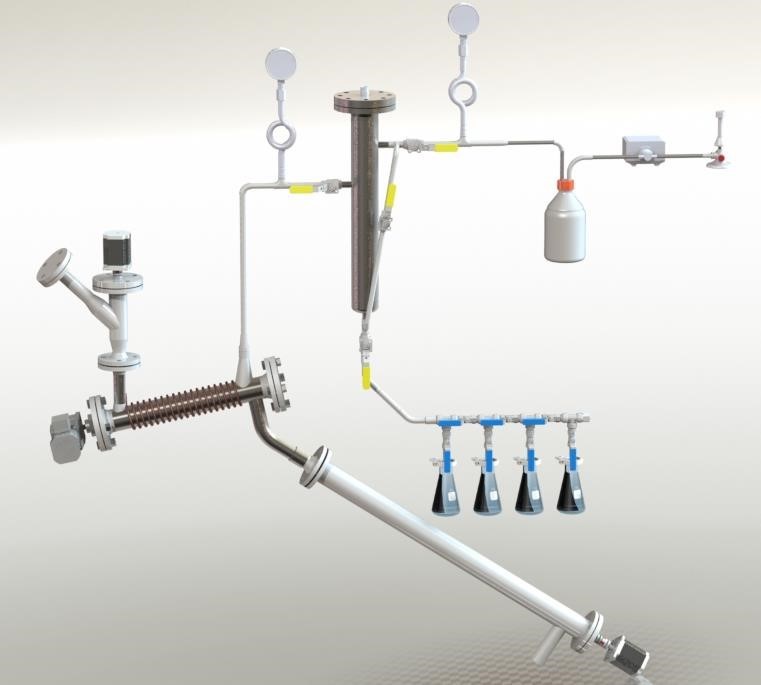
Energetické využití vytříděného komunálního odpadu
Úvod
V současné době se nejvíc experimentů a testů na laboratorní jednotce řeší s vytříděným komunálním odpadem.
Objemy jednotlivých získaných produktů (frakcí) po termické depolymerizaci nezávisí jen na složení a vlastnostech vstupní suroviny, ale i na procesních podmínkách během vlastní depolymerizace, např. forma vstupního materiálu (granulometrie), typ a velikost depolymerizační jednotky, procesní teplota, rychlost ohřevu, doba zdržení (čas expozice materiálu v dané teplotě), hydrodynamické podmínky, ostatní výbava depolymerizační jednotky zejména typ kondenzátorů (chladičů) atd. Jednotlivé hmotnostní objemy získaných produktů depolymerizace odpadních materiálů se v závislosti na popsaných podmínkách pohybují v rozsahu:
- procesní plyn (5 až 28 hm.%)
- procesní olej (30 až 55 hm.%)
- procesní tuhý inertní zbytek (28 až 45 hm.%)
Poměry získaného procesního plynu a oleje, lze v omezeném rozsahu řízeně regulovat nastavením vhodných procesních parametrů, které vyhovují záměru a potřebám provozovatele.
Získané procesní produkty
Pevný inertní zbytek obsahuje uhlík v anorganické podobě, popeloviny a minerální látky, které jsou přítomné ve vstupním materiálu od začátku. Tento pevný anorganický uhlík je možné využít v chemickém průmyslu, dále lze jeho demineralizací a následnou aktivací vyrobit aktivní uhlí s porovnatelným měrným povrchem jako komerčně vyráběně aktivní uhlí, nebo se dá taktéž využít jako ekologicky čisté palivo, nebo jako nosič NPK a hydro-sorpční materiál pro půdní aplikaci.
Kapalný procesní olej je komplexní směsí uhlovodíků C5 – C40, někdy s obsahem aromatických uhlovodíků. Takto získaná olejová frakce se může použít přímo jako palivo, např. jako topný olej v kotlích, popř. jako palivo pro generátory, nebo motory jakožto substitut motorové nafty, nebo jako vstupní surovina pro petrochemický průmysl, nebo jako zdroj velmi cenných chemikálií po dalším zpracování.
Procesní plyn je podíl získaných produktů termické depolymerizace, který je složený hlavně z H2, H2S, CO, CO2, CH4, C2H4 a takto získaný procesní plyn je látka s vysokým energetickým potenciálem (kormě CO2). Vzhledem k energetické vydatnosti získaného procesního plynu a taktéž pro jeho obtížnou skladovatelnost a stlačitelnost je tento podíl obvykle používán jako palivo pro přímé využití k výrobě elektrické energie především pro krytí vlastní spotřeby elektrické energie depolymerizační jednotky, popř. k výrobě převisu elektrické energie a tepelné energie jako vedlejšího produktu energobloku, který kladně ovlivňuje celkovou účinnost provozu depolymerizační technologie.
Experiment
Při řešení experimentálních testů na laboratorní jednotce, jsme vycházely z parametrů složení vzorků.
pol. | Frakce měrná hmotnost [kg/m3] | výhřevnost [MJ/kg] | sypná hmotnost [kg/m3] |
1. Papír (směs) | 1000 | 14,11 | 431 |
2. Textil | 1400 | 16 | 450 |
3. TetraPack | 980 | 25 | 520 |
4. PET | 1390 | 27 | 407 |
5. Plasty (směs) | 1250 | 35 | 769 |
6. Guma | 1200 | 34,92 | 673 |
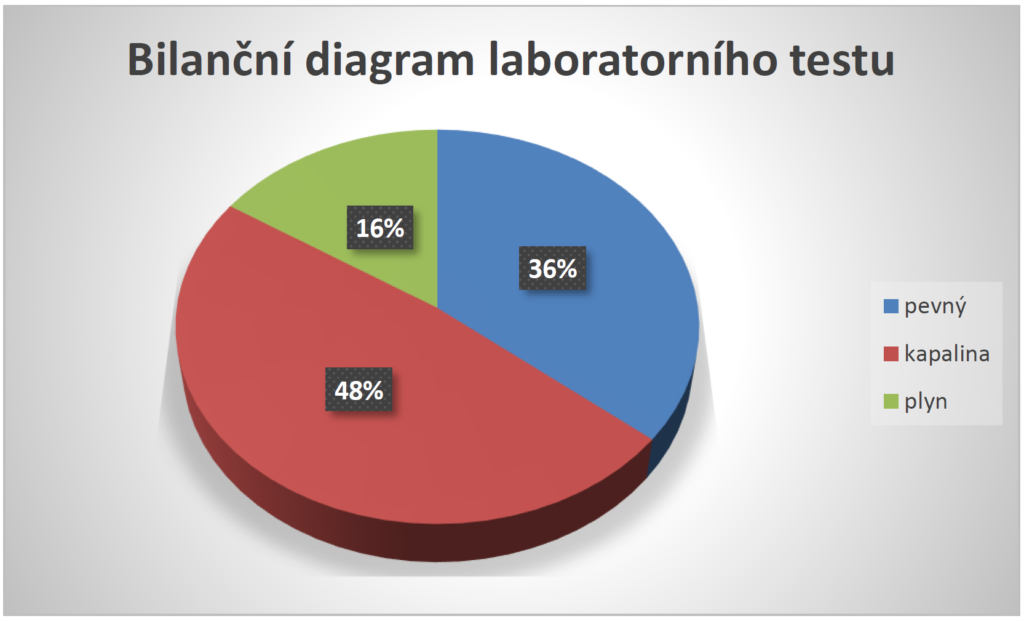
Po sérii laboratorních testů dochází k validačnímu testu na poloprovozní jednotce v Dubenci u Příbrami.
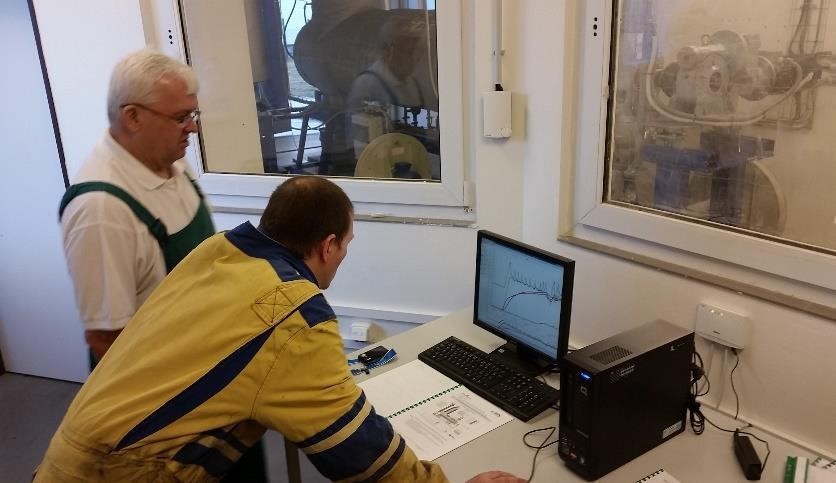
Realizace
Technologie termické depolymerizace, vyrobena v souladu se Směrnicí evropského parlamentu a rady č. 46/2006 ES, v souladu s Nařízením vlády č. 176/2008 Sb. ve znění pozdějších předpisů a v souladu s ostatními související právními a technickými normami, byla vyvinuta a konstruována jako technologie bezodpadová, tzn. že veškeré získané produkty termické depolymerizace lze beze zbytku bezpečně a smysluplně využít a taktéž jako technologie bez trvalé potřeby vnějšího zdroje energie pro svůj provoz. V případě získaného procesního plynu je téměř vždy, vzhledem k jeho obtížné skladovatelnosti a stlačitelnosti, využíván jako palivo s vysokým energetickým potenciálem pro čistý provoz energobloku.
V případě získaného procesního oleje a uhlíku mimo jiných možností, které jsou uvedeny výše, lze tyto produkty využít jako výborný obchodní artikl.
Technologie je konstruována se standardní velikostí retorty (reaktoru) 610 * 6500 * 8 mm se vstupním výkonem 1.000 kg/hod. (platí pro materiál se sypnou hmotností 750 kg/m3), která je ohřívána úsporným čtyřzónovým indukčním ohřevem s aktivní elektronickou termostatickou regulací.
Jednotka DEPO je členěna do 7 modulů
- Modul A
- Modul B
- Olejové hospodářství
- Plynové hospodářství
- Energoblok
- Bezpečnostní fléra
- Velín technologie
Modul „A“ – Retorta a příslušenství
Při návrhu a vlastní konstrukci zařízení byl kladen velký důraz na kontinuálnost, spolehlivost a efektivnost, ale především na bezpečnost provozu. Pro splnění všech těchto předpokladů je aplikován bezobslužný šroubový systém plnění retorty s napojením na externí zásobovací cesty pro vstupní materiál s propojenými řídícími a sdělovacími okruhy. Tento systém umožnuje kontinuální bezporuchový provoz plnění retorty a zabezpečuje dokonalou vzduchotěsnost prostředí depolymerizace. Pro zvýšení bezpečnosti, spolehlivosti a účinnosti provozu termické depolymerizace je v této části instalováno zařízení umožňující dávkování jinak neškodného inertního plynu do směsi vstupního materiálu, aby se zabezpečilo dokonalé anaerobní prostředí pro proces depolymerizace bez přístupu okysličovadel.
Vlastní retorta umožnuje dlouhodobý kontinuální provoz díky šroubovému posunu materiálu ve vnitřním prostoru retorty. Tento pomaluběžný šroubový posun se samočistícím efektem je poháněn přes izolační můstek převodovou skříní s elektromotorem. Elektromotor je rovněž elektronicky řízen v závislosti na vyhodnocování důležitých parametrů provozu automaticky a v omezeném bezpečném rozsahu zásahem obsluhy. Retorta je dokonale tepelně odizolována minerálními izolačními vrstvami, aby byly minimalizovány případné tepelné ztráty při jejím ohřevu. Kolem retorty jsou navinuty čtyři nezávislé indukční cívky v ochranné stínící kleci, které s vysokou rychlostí a účinností řízeně zahřívají plášť retorty i vnitřní šroubový posun na požadovanou teplotu.
V plášti retorty jsou instalovány odolné a přesné teplotní senzory. Pro zvýšení spolehlivosti a bezpečnosti jsou instalovány párově. Elektronickým řídícím systémem jsou údaje vyhodnocovány a komparovány vždy z obou čidel na každé ze čtyř zón. Při jakékoli anomálii je tento stav signalizován, nebo např. při výpadku signálu ze senzoru je proces depolymerizace bezpečně odstaven. Tato eventualita je však pouze teoretická.
Retorta je opatřena dvěma výstupy. Výstup na vrchní části retorty je určen pro odvod vyvíjeného procesního plynu nasyceného aerosolovými kapénkami. Tato směs je odsávána výkonným dmychadlem s řízeným podtlakem (podrobněji pospáno níže v části kondenzace). Výstup v koncové spodní části retorty je určen pro výstup čistého inertního zbytku bez obsahu těkavých látek. Kontinuální vynášení inertního zbytku ve formě prášku je prováděno opět bezobslužným šroubovým systémem zajišťující bezporuchový provoz a dokonalou vzduchotěsnost prostředí depolymerizace. Tento vynášecí systém je vybaven kompaktním chlazením pláště šroubového systému, který spolehlivě ochladí inertní zbytek na bezpečnou teplotu, při které nehrozí jeho případné vznícení na výstupu. Proces chlazení a výstupní teploty inertního pevného zbytku je opět sledován příslušnými ovládacími a sdělovacími okruhy a spojen s nadřazeným řídícím systémem.
Vynášení inertního zbytku může být vybaveno dalším fakultativním zařízením, např. separaci kovů, plnění do přepravních vaků, atd.
Systém kontinuálního plnění retorty, vlastní retorta, vyrobená z tepelně i chemicky nejodolnějších materiálů se všemi prvky ohřevu, a kontinuální systém vynášení a chlazení pevného zbytku, jsou uzavřeny v upraveném kontejneru ISO40 s charakteristickým designem konstrukce. Vnitřní prostor kontejneru je klimatizován. Za provozu je kontejner modulu „A“ z bezpečnostních důvodů znepřístupněn obsluze a monitorován sofistikovanou zabezpečovací technikou, která při zjištění případné provozní anomálie dokáže bez zásahu obsluhy korigovat některé parametry procesu a navrátit je do normálního provozního stavu, nebo zařízení bezpečně odstavit naprogramovanou vypínací sekvencí. V krajním případě, např. při nebezpeční požáru v bezprostředním okolí retorty, zabezpečovací zařízení aktivuje protipožární systém a vnitřní prostor kontejneru zaplní inertním plynem, znemožní tak zahoření a zabrání větším škodám.
Modul „B“ – Kondenzdace
Výše popsaná tzv. aktivní část termické depolymerizace, tj. retorta s příslušenstvím, je kompaktně spojena s blokem kondenzace, která je taktéž místěna v upraveném kontejneru ISO20. Zde je umístěno výkonné dmychadlo, jehož výkon je ovládán a řízen elektronicky s rychlou odezvou na signály instalovaných podtlakových senzorů. Řízení podtlaku v celém systému depolymerizace je důležitým faktorem, který výrazně ovlivňuje kvalitu získaného procesního plynu, ale zejména procesního oleje. Dmychadlo odsává vznikající páry z retorty přes třístupňovou horkou velkoplošnou kondenzaci, která dokáže s vysokou účinností až 99 % odseparovat z plynné frakce aerosoly procesního oleje. Získaný procesní olej stéká do chlazené olejové nádrže pod kondenzátory, odtud je pak cyklicky odčerpáván do vnějších olejových zásobníků, ze kterých je přes stáčecí zařízení připraven k expedici. Získaný procesní plyn, které je zbaven aerosolové složky je dále nasáván přes vícestupňovou úpravnu plynu, kde dochází k jeho závěrečné úpravě, filtraci a dosušení. Dmychadlo následně ukládá čistý plyn do plynojemu s objemem 500 m3, který slouží jako zásobní rezervoár plynného paliva pro provoz energobloku.
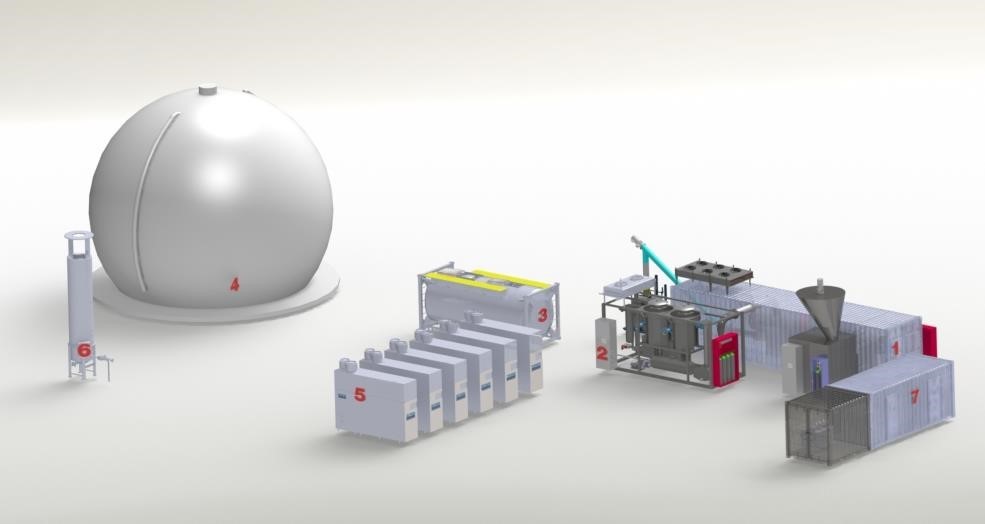
Závěr
Z dosud provedených rozborů a analýz je zjevné, že se naše firma dala na správnou cestu energetického využití odpadů.